Der sichere Umgang mit Industriegasen ist von entscheidender Bedeutung für den reibungslosen Betrieb in der industriellen Produktion. Gase wie Sauerstoff, Stickstoff, Wasserstoff und Argon werden häufig verwendet, um verschiedene Prozesse zu unterstützen und zu optimieren. Ihre spezifischen Eigenschaften und potenziellen Gefahren erfordern jedoch sorgfältige Sicherheitsvorkehrungen. Ein umfassendes Sicherheitsmanagementsystem, das die Eigenschaften der Gase, geeignete Lagerbedingungen, regelmäßige Wartung und die Schulung der Mitarbeiter umfasst, ist unerlässlich, um Risiken zu minimieren und die Gesundheit der Mitarbeiter zu gewährleisten.
Eigenschaften von Industriegasen verstehen
In der industriellen Produktion werden verschiedene Arten von Gasen verwendet, von denen jede ihre eigenen Eigenschaften hat. Das Verständnis der Eigenschaften jedes Industriegases ist entscheidend für sichere Lagerung und Verwendung. Hier sind einige häufige Industriegase und ihre Eigenschaften sowie Sicherheitsmanagementpunkte:
Sauerstoff (O2)
Sauerstoff ist ein häufig verwendetes Industriegas, das für Oxidations-, Verbrennungs- und Redoxreaktionen sowie für viele andere industrielle Prozesse verwendet wird. Sauerstoff ist jedoch auch ein starkes Oxidationsmittel und kann bei Kontakt mit brennbaren Stoffen zu Bränden oder Explosionen führen. Daher müssen beim Lagern und Verwenden von Sauerstoff folgende Sicherheitsmaßnahmen beachtet werden:
- Mischen mit brennbaren Stoffen ist verboten, um Brände oder Explosionen zu vermeiden.
- Verwenden Sie spezielle Sauerstoffflaschen, um Dichtigkeit und Stabilität zu gewährleisten.
- Überprüfen Sie regelmäßig Sauerstoffleitungen und Ventile, um Gaslecks zu vermeiden.
- Vermeiden Sie den Kontakt von Sauerstoff mit Ölen oder Schmiermitteln unter hohen Temperaturen oder Drücken, um Selbstentzündung oder Explosionen zu verhindern.
Stickstoff (N2)
Stickstoff ist ein inerten Gas, das in der industriellen Produktion häufig zur Atmosphärenkontrolle, zur Verhinderung von Oxidationen und Redoxreaktionen usw. verwendet wird. Obwohl Stickstoff selbst nicht brennbar oder giftig ist, kann er bei hohen Konzentrationen zu Erstickungsgefahr führen. Daher sollten bei der Sicherheitsverwaltung von Stickstoff folgende Punkte beachtet werden:
- Stellen Sie sicher, dass Lagerbereiche gut belüftet sind, um die Ansammlung von Stickstoff und damit verbundene Erstickungsunfälle zu verhindern.
- Vermeiden Sie Stickstofflecks und überprüfen Sie regelmäßig die Dichtigkeit von Gasflaschen und -leitungen.
- Verhindern Sie den Kontakt von Stickstoff mit brennbaren oder leicht entzündlichen Stoffen, um Brände oder Explosionen zu vermeiden.
Wasserstoff (H2)
Wasserstoff ist ein leicht entzündliches Gas, das bei Kontakt mit Luft oder Sauerstoff eine brennbare Mischung bilden kann, die leicht zu Explosionen führen kann. Daher sind beim Lagern und Verwenden von Wasserstoff besondere Sicherheitsvorkehrungen erforderlich:
- Verwenden Sie spezielle Wasserstoffflaschen und stellen Sie sicher, dass Lagerbereiche gut belüftet sind.
- Überprüfen Sie regelmäßig Wasserstoffleitungen und Ventile, um Gaslecks zu vermeiden.
- Mischen Sie Wasserstoff nicht mit Sauerstoff oder anderen Oxidationsmitteln, um Explosionsunfälle zu vermeiden.
Argon (Ar)
Argon ist ein inertes Gas, das häufig in industriellen Prozessen wie Schutzgas-Schweißen, Metallbearbeitung und Atmosphärenkontrolle verwendet wird. Argon ist selbst nicht leicht entzündlich und auch nicht giftig, kann jedoch bei hohen Konzentrationen zu Erstickungsgefahr führen. Daher sollten beim Umgang mit Argon folgende Sicherheitsmaßnahmen beachtet werden:
- Lagerbereiche sollten gut belüftet sein, um eine Ansammlung von Argon und damit verbundene Erstickungsunfälle zu verhindern.
- Vermeiden Sie Argonlecks und überprüfen Sie regelmäßig die Dichtheit von Lagergeräten und -leitungen.
- Verhindern Sie den Kontakt von Argon mit Zündquellen oder brennbaren Stoffen, um Brände oder Explosionen zu vermeiden.
Das Verständnis der Eigenschaften von Industriegasen ist entscheidend für sichere Lagerung und Verwendung. Durch die Umsetzung entsprechender Sicherheitsmaßnahmen entsprechend den Eigenschaften der Gase können Gaslecks, Brände, Explosionen und Erstickungsunfälle wirksam vermieden werden, um die Produktionssicherheit und die Gesundheit der Mitarbeiter zu gewährleisten.
Standards für die Lagerumgebung festlegen
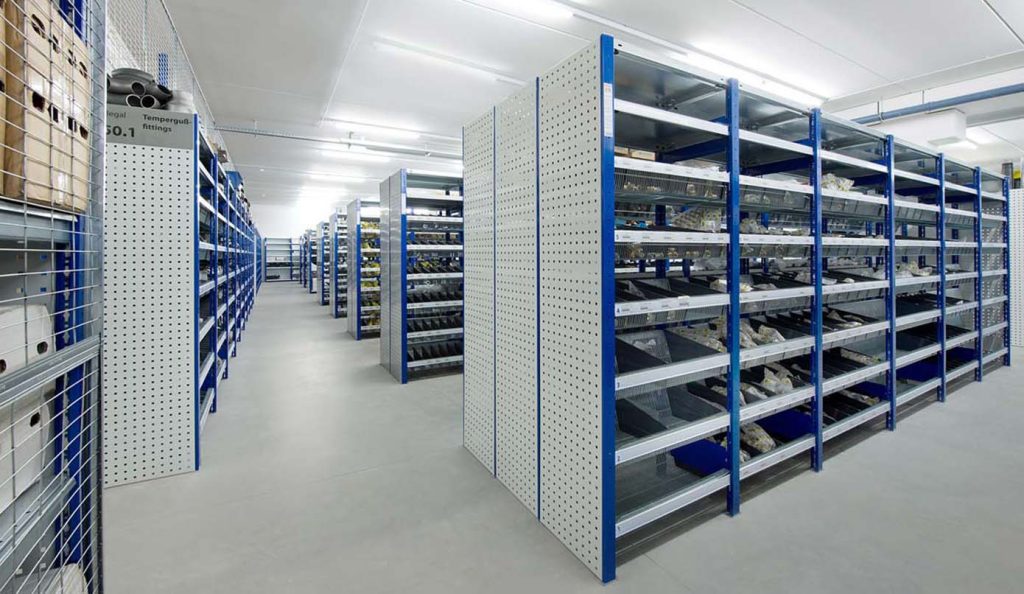
Die Lagerumgebung für Industriegase ist ein entscheidender Schritt, um die sichere Lagerung und Verwendung von Gasen zu gewährleisten, und ihr Standard beeinflusst direkt die Produktionssicherheit und -effizienz. Eine qualifizierte Lagerumgebung muss die Eigenschaften des Gases, die Leistung der Lagergeräte und die Umgebungsfaktoren des Lagerbereichs ganzheitlich berücksichtigen.
Der Bereich zur Lagerung von Gasen muss von jeglichen potenziellen Zündquellen wie offenen Flammen, Funken, Wärmequellen usw. entfernt sein. Der Kontakt von Gasen mit Zündquellen kann zu Bränden oder Explosionen führen. Daher sollten entsprechende Brandschutzbereiche eingerichtet werden, um sicherzustellen, dass zwischen der Zündquelle und dem Gas ausreichend Sicherheitsabstand besteht. Gleichzeitig sollte sichergestellt werden, dass der Lagerbereich von heißen Bereichen ferngehalten wird, um das Risiko von Gasüberhitzung und damit verbundenen Lecks und Explosionen zu minimieren.
Direkte Sonneneinstrahlung kann dazu führen, dass die Behälter für die Lagerung von Gasen erwärmt werden, was den Druck des Gases erhöht und das Risiko von Lecks erhöht. Daher sollte direkte Sonneneinstrahlung vermieden werden, indem Sonnenschirme aufgestellt oder schattige und gut belüftete Bereiche ausgewählt werden. Insbesondere im Freien gelagerte Gase müssen den Einfluss direkter Sonneneinstrahlung berücksichtigen, um die Stabilität und Sicherheit der Lagerumgebung zu gewährleisten.
Die Lagerbereiche müssen gut belüftet sein, um eine Ansammlung von Gasen und damit verbundene Sicherheitsrisiken zu vermeiden. Das Belüftungssystem sollte sorgfältig gestaltet sein, um eine rechtzeitige Ableitung und Erneuerung der Gase im Lagerbereich sicherzustellen und eine zu hohe Gas-Konzentration zu verhindern, die zu Erstickung oder Explosion führen kann. Darüber hinaus sollten Lagerbereiche regelmäßig von Unrat und Staub befreit werden, um eine gute Luftzirkulation zu gewährleisten und das Risiko von Bränden und Explosionen zu verringern.
Lagergeräte wie Gasflaschen, -tanks usw. müssen fest und zuverlässig in den dafür vorgesehenen Lagerbereichen befestigt sein, um zu verhindern, dass die Geräte umkippen oder zusammenbrechen und Gaslecks oder andere Sicherheitsunfälle verursachen. Die Sicherheit und Stabilität der Lagergeräte haben direkten Einfluss auf die Sicherheit und Stabilität der Lagerumgebung. Daher müssen Lagergeräte regelmäßig überprüft und gewartet werden, um sicherzustellen, dass sie sich in gutem Arbeitszustand befinden.
Die Lagerbereiche sollten regelmäßig auf Sicherheitsmängel überprüft und vorhandene Sicherheitsrisiken rechtzeitig beseitigt werden. Die Sicherheitsprüfung umfasst unter anderem Brandschutzrisiken, Gaslecks, Geräteschäden usw. Bei Feststellung von Problemen müssen sofort entsprechende Reparatur- oder Verbesserungsmaßnahmen ergriffen werden, um sicherzustellen, dass die Lagerumgebung den Sicherheitsanforderungen entspricht. Die Sicherheitsprüfung sollte von Fachleuten durchgeführt werden und klare Aufzeichnungen und Nachverfolgungsmaßnahmen haben, um sicherzustellen, dass Sicherheitsprobleme rechtzeitig behoben werden.
Eine standardisierte Lagerumgebung ist die Grundlage für die sichere Lagerung und Verwendung von Industriegasen. Durch Maßnahmen wie die Vermeidung von Zündquellen und Hitze, den Schutz vor direkter Sonneneinstrahlung, die Aufrechterhaltung einer guten Belüftung, die Sicherung von Lagergeräten und regelmäßige Sicherheitsinspektionen können Risiken von Sicherheitsunfällen während der Lagerung von Industriegasen wirksam reduziert werden, um die Produktionssicherheit und die Gesundheit der Mitarbeiter zu gewährleisten.
Verwendung geeigneter Lagerausrüstung
Die Auswahl geeigneter Lagerausrüstung ist ein entscheidender Schritt, um die sichere Lagerung und Verwendung von Industriegasen zu gewährleisten. Unterschiedliche Gase erfordern unterschiedliche Lagerausrüstungen, und die Qualität und Leistung der Lagerausrüstung beeinflussen direkt die Sicherheit und Stabilität der Gaslagerung.
Gasflaschen und Gasbehälter sind gängige Behälter zur Lagerung von Industriegasen, und ihre Auswahl hängt von Faktoren wie den Eigenschaften des Gases, den Druckanforderungen und der Lagerumgebung ab. Im Allgemeinen eignen sich Gasflaschen zur Lagerung von Gasen mit höherem Druck wie Sauerstoff, Wasserstoff usw., während Gasbehälter zur Lagerung von Gasen mit niedrigerem Druck wie Stickstoff, Argon usw. geeignet sind.
Gasflaschen bestehen in der Regel aus Stahl oder Aluminium und weisen eine gute Druckbeständigkeit und Dichtheit auf. Gasbehälter werden hauptsächlich aus Stahl oder Kunststoff hergestellt und bieten eine größere Kapazität und Stabilität. Bei der Auswahl von Lagerbehältern muss sichergestellt werden, dass sie die richtige Größe und Kapazität haben und den Anforderungen des Arbeitsplatzes entsprechen.
Die Auswahl der Lagerausrüstung muss die Lagerumgebung und die Sicherheitsanforderungen berücksichtigen. Zum Beispiel erfordert eine Umgebung mit hoher Temperatur die Auswahl von hitzebeständigen Lagerbehältern und Maßnahmen zur Kühlung, um die Stabilität der Gase aufrechtzuerhalten. In feuchten Umgebungen müssen rost- und korrosionsbeständige Materialien ausgewählt werden, um die Lebensdauer und Sicherheit der Behälter zu gewährleisten.
Darüber hinaus ist die Sicherheitsleistung der Lagerausrüstung ein entscheidender Auswahlfaktor. Zertifizierte Markenprodukte sollten bevorzugt werden, um sicherzustellen, dass sie den relevanten Sicherheitsstandards und Vorschriften entsprechen. Gleichzeitig sollten Lagerausrüstungen regelmäßig überprüft und gewartet werden, um Sicherheitsrisiken rechtzeitig zu erkennen und zu beheben und einen sicheren und zuverlässigen Betrieb zu gewährleisten.
Bei der Verwendung von Lagerausrüstungen müssen auch wirksame Schutzmaßnahmen ergriffen werden, um Gaslecks und Sicherheitsunfälle zu verhindern. Zum Beispiel sollten für Hochdruck-Gaslagerausrüstungen Sicherheitsventile und Druckentlastungseinrichtungen installiert werden, um überschüssiges Gas rechtzeitig freizusetzen und eine Geräteexplosion zu verhindern. Für brennbare Gaslagerausrüstungen sollten Maßnahmen zum Brandschutz ergriffen werden, um eine sichere Verwendung zu gewährleisten.
Die Auswahl geeigneter Lagerausrüstung ist ein wichtiger Schutz für die sichere Lagerung und Verwendung von Industriegasen. Durch die Auswahl geeigneter Lagerbehälter, die Berücksichtigung der Lagerumgebung und der Sicherheitsanforderungen sowie die Umsetzung wirksamer Schutzmaßnahmen können Risiken von Sicherheitsunfällen während der Gaslagerung effektiv reduziert werden, um die Produktionssicherheit und die Gesundheit der Mitarbeiter zu gewährleisten.
Regelmäßige Inspektion und Wartung der Ausrüstung
Die regelmäßige Inspektion und Wartung der Lagerausrüstung ist ein unverzichtbarer Schritt, um die sichere Lagerung und Verwendung von Industriegasen zu gewährleisten. Regelmäßige Wartung stellt nicht nur den normalen Betrieb der Ausrüstung sicher, sondern hilft auch dabei, potenzielle Sicherheitsrisiken rechtzeitig zu erkennen und zu beheben, um Unfälle wirksam zu verhindern.
Die Dichtleistung ist einer der Schlüsselfaktoren, um die Stabilität der gelagerten Gase zu gewährleisten. Es ist äußerst wichtig, die Dichtleistung der Lagerausrüstung regelmäßig zu überprüfen. Dazu gehört die Überprüfung, ob an den Dichtstellen, Ventilen und Rohrverbindungen von Gasflaschen oder Gasbehältern Lecks auftreten. Bei der Inspektion können Seifenwasser oder Gasdetektoren verwendet werden, um potenzielle Lecks zu erkennen. Sobald ein Leck festgestellt wird, müssen sofort Maßnahmen zur Reparatur ergriffen werden, um sicherzustellen, dass kein Gas austritt und keine Sicherheitsrisiken entstehen.
Die flexible Bedienung der Ventile ist entscheidend für die Kontrolle des Gasflusses und -drucks. Es ist wichtig, die Ventile der Lagerausrüstung regelmäßig zu überprüfen, einschließlich der Hauptventile und Sicherheitsventile, um sicherzustellen, dass sie flexibel und reibungslos funktionieren. Wenn Ventile klemmen, lecken oder beschädigt sind, müssen sie sofort repariert oder ersetzt werden, um den sicheren Betrieb der Ausrüstung zu gewährleisten.
Beschädigungen der Oberfläche von Gasflaschen können deren Druckbeständigkeit und Dichtleistung beeinträchtigen und das Risiko von Gaslecks und Explosionen erhöhen. Es ist notwendig, die Oberfläche der Gasflaschen regelmäßig auf Dellen, Kratzer oder Rost zu überprüfen und diese bei Bedarf zu reparieren oder auszutauschen. Außerdem sollten die Kennzeichnungen und Schilder der Gasflaschen überprüft werden, um sicherzustellen, dass sie vollständig und lesbar sind, damit die Art und Spezifikation der Gasflaschen korrekt identifiziert werden können.
Die Erstellung eines umfassenden Wartungsplans ist eine wichtige Maßnahme, um sicherzustellen, dass regelmäßige Inspektionen und Wartungsarbeiten effektiv durchgeführt werden. Entsprechend der Nutzung und den Anforderungen der Ausrüstung sollte ein entsprechender Wartungsplan erstellt werden, der die Inspektionshäufigkeit, den Wartungsinhalt und die verantwortlichen Personen festlegt. Darüber hinaus sollte eine vollständige Wartungsdokumentation geführt werden, in der jede Inspektion und Wartung mit Inhalt, Ergebnissen und Maßnahmen festgehalten wird, um den Betriebszustand der Ausrüstung zu verfolgen und potenzielle Probleme zu erkennen.
Die regelmäßige Inspektion und Wartung der Ausrüstung ist ein entscheidender Schritt, um die sichere Lagerung und Verwendung von Industriegasen zu gewährleisten. Durch die Überprüfung der Dichtleistung der Ausrüstung, der Ventilfunktion und der Oberflächenbeschädigungen der Gasflaschen sowie durch die rechtzeitige Behebung von Problemen können Gaslecks, Brände und Explosionen wirksam verhindert und die Produktionssicherheit und Gesundheit der Mitarbeiter sichergestellt werden.
Aufbau eines umfassenden Sicherheitsmanagementsystems
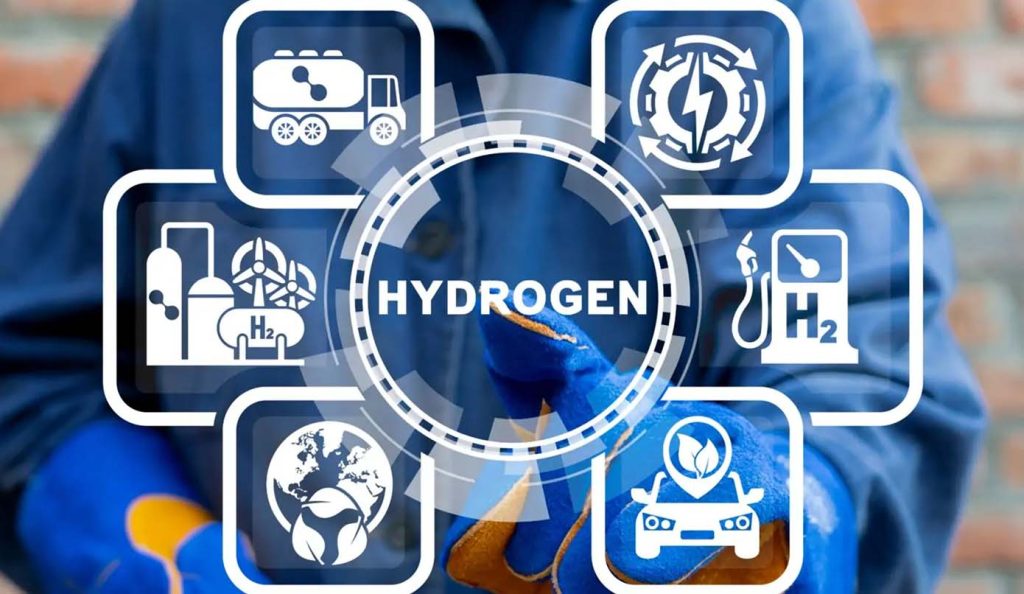
Der Aufbau eines umfassenden Sicherheitsmanagementsystems ist eine wichtige Maßnahme, um die sichere Lagerung und Verwendung von Industriegasen zu gewährleisten. Ein vollständiges Sicherheitsmanagementsystem kann nicht nur den Prozess der Gaslagerung und -verwendung regeln, sondern auch das Sicherheitsbewusstsein und die Notfallkompetenz der Mitarbeiter verbessern und so Unfälle wirksam verhindern und bewältigen.
Der Aufbau eines umfassenden Sicherheitsmanagementsystems beginnt mit der Erstellung eines Sicherheitsausbildungsplans. Die Sicherheitsausbildung sollte Schulungen über die Eigenschaften und Gefahren von Industriegasen, sichere Betriebsverfahren sowie Notfallpläne und Unfallmanagementprozesse umfassen. Die Schulungsinhalte sollten nach den unterschiedlichen Positionen der Mitarbeiter kategorisiert werden, um sicherzustellen, dass jeder Mitarbeiter die Sicherheitsrisiken seiner Arbeit kennt und die entsprechenden Schutzmaßnahmen und Fähigkeiten beherrscht.
Sichere Betriebsverfahren sind ein wesentlicher Bestandteil des Sicherheitsmanagementsystems. Für verschiedene Arten von Industriegasen und unterschiedliche Arbeitsszenarien sollten detaillierte sichere Betriebsverfahren entwickelt werden, die den Arbeitsablauf, Sicherheitsvorkehrungen und Notfallmaßnahmen klar definieren. Die Bediener müssen die sicheren Betriebsverfahren strikt einhalten, um sicherzustellen, dass während des Produktionsprozesses keine Unfälle passieren.
Ein Notfallplan ist ein weiterer wesentlicher Bestandteil des Sicherheitsmanagementsystems und eine wirksame Maßnahme zur Bewältigung von Vorfällen und Notfällen. Für mögliche Sicherheitsunfälle sollten entsprechende Notfallpläne erstellt werden, die den Notfallprozess, die Verantwortlichen und die Ressourcenzuweisung festlegen. Regelmäßige Übungen und Schulungen sollten organisiert werden, um die Notfallreaktionsfähigkeit und Teamkooperationsfähigkeit der Mitarbeiter zu verbessern.
Der Aufbau eines umfassenden Sicherheitsmanagementsystems erfordert auch eine verstärkte Sicherheitsüberwachung und -aufsicht. Durch die Einrichtung einer Sicherheitsabteilung oder eines Ausschusses, der für die Organisation, Koordination und Überwachung der Sicherheitsmanagementarbeit verantwortlich ist, können regelmäßige Sicherheitsinspektionen und -bewertungen durchgeführt werden. Probleme müssen rechtzeitig behoben werden, um die wirksame Umsetzung und Einhaltung des Sicherheitsmanagementsystems sicherzustellen.
Die Stärkung der Sicherheitsaufklärung ist ein wichtiger Weg, um das Sicherheitsbewusstsein und die Kompetenz der Mitarbeiter zu erhöhen. Regelmäßige Sicherheitsschulungen und Bildungsaktivitäten sollten organisiert werden, um den Mitarbeitern Sicherheitswissen und -fähigkeiten zu vermitteln, ihr Sicherheitsbewusstsein und ihre Präventionsfähigkeit zu stärken. Durch verschiedene Formen und Kanäle sollte die Sicherheitsaufklärung intensiviert werden, um eine Sicherheitskultur zu schaffen und das Sicherheitsmanagementsystem wirksam umzusetzen.
Der Aufbau eines umfassenden Sicherheitsmanagementsystems ist eine wichtige Maßnahme, um die sichere Lagerung und Verwendung von Industriegasen zu gewährleisten. Durch die Erstellung von Sicherheitsausbildungsplänen, sicheren Betriebsverfahren und Notfallplänen, die Verstärkung der Sicherheitsüberwachung und -aufsicht sowie die Intensivierung der Sicherheitsaufklärung können das Sicherheitsbewusstsein und die Notfallkompetenz der Mitarbeiter verbessert, Sicherheitsunfälle wirksam verhindert und bewältigt und die Produktionssicherheit und Gesundheit der Mitarbeiter gewährleistet werden.